La sicurezza sul lavoro ed una buona progettualità dei flussi produttivi sono elementi che scaturiscono da una intensa progettualità. Quando la progettualità non basta, però, si può tentare di andare oltre grazie alla realtà aumentata: è questa la convinzione di Ford, che nello sviluppo delle nuove vetture si è affidata ad una serie di simulazioni digitali che consentono di capire in anteprima se ogni processo sia stato o meno ottimizzato in funzione dell’opera dell’uomo all’interno delle linee di montaggio.
Le tecniche odierne sono frutto di una ricerca che va avanti fin dal 2003, quando l’Ovale Blu maturò la convinzione per cui una miglior progettualità delle fasi di lavoro avrebbe sostanzialmente evoluto la produzione stessa, ottimizzato le condizioni di lavoro e ridotto incidenti e infortuni. A distanza di anni i risultati sono conclamati e il processo di ricerca sta continuando, sfiorando la realtà virtuale per raccogliere un maggior numero di riscontri sul campo prima di portare all’interno della linea i nuovi processi di montaggio e i nuovi macchinari di lavorazione.
Gli investimenti del passato sono andati nella direzione dell’eliminazione dei gesti a bassa ergonomia, potenzialmente logoranti nel lungo periodo e non ottimali ai fini del miglior funzionamento dei processi di linea. Oggi tutto ciò evolve però ad un nuovo livello, così come spiegato dal responsabile Allison Stephens: «Avvalendoci di test digitali sull’ergonomia dei movimenti, da anni rendiamo più sicure le nostre strutture sempre e più agevole il lavoro dei nostri dipendenti».
Grazie alle simulazioni virtuali, Ford è, infatti, in grado di sperimentare in anticipo l’ergonomia delle linee di montaggio e applicare metodi di riduzione degli sforzi e tecniche di prevenzione degli infortuni sul lavoro con precisione sempre maggiore, al fine di incrementare la sicurezza dei dipendenti sulla base delle effettive condizioni operative.
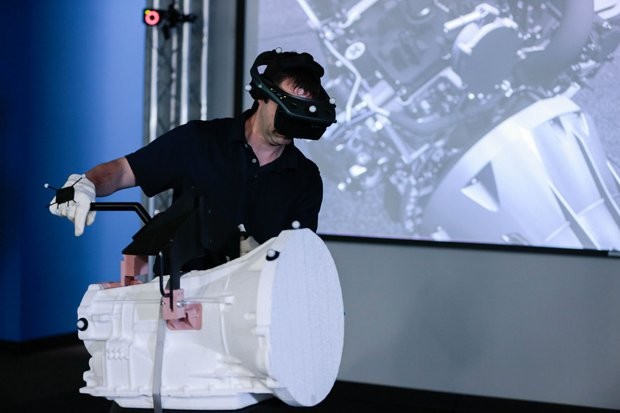
Fabbrica virtuale di Ford
Stampa 3D e realtà aumentata
In preparazione al lancio di ogni nuovo modello (ivi comprese le nuove Mustang), Ford opera fino a 900 simulazioni digitali all’interno di una fase di training che può durare dai 2 ai 3 anni: ogni singolo movimento viene analizzato e testato, così che dalla raccolta dati si possa arrivare ad una linea perfetta attraverso studi e soluzioni ingegneristici.
Per dar vita a questo tipo di simulazioni, Ford si avvale di componenti stampati in 3D e ambienti immersivi completamente virtuali, ricreando fedelmente l’ambito di lavoro per simulare totalmente il contesto con massima verosimiglianza. I test vengono quindi svolti con sistemi di motion-capture che sfruttano telecamere 3D per catturare e digitalizzare ogni singolo spostamento registrato nel campo visivo; i partecipanti al test, nella fattispecie, utilizzano tute arricchite con 52 punti di riferimento che rendono più fedele e capillare il monitoraggio. La virtualizzazione di queste fasi consente di ottimizzare i processi in modo più rapido, potendo contare su di una raccolta dati più puntuale e senza doversi basare in modo empirico sull’esperienza o su situazioni successive alla messa a dimora della linea produttiva.
Analizzandone il movimento, il computer è in grado di misurare lo stress muscolare, gli effetti sulle giunture e sull’equilibrio del corpo durante il lavoro.
Studi nati per il perfezionamento delle performance sportive diventano dunque ora campi di applicazione per l’ottimizzazione dei processi produttivi: «La medesima tecnologia aiuta Ford a sviluppare ambienti di lavoro che rappresentano lo stato dell’arte in termini di sicurezza e comodità per i propri dipendenti».